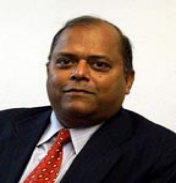
Keynote Speaker
Prof. Ramesh K. Agarwal
Washington University in St. Louis, USA
Speech title: Numerical Analysis of Propeller-Wing Interaction in a UAV with Distributed Electric Propulsion
Abstract: As battery and electric motor technology continues to advance rapidly, propeller-driven electric UAV/aircraft are likely to become a significant part of the aviation market in the near future. One proposed design configuration for electric UAV involves using large, wing-tip mounted propellers to actively cancel wingtip vortices; a method called active wingtip vortex cancellation (AWVC). By reclaiming part of the kinetic energy that would otherwise be lost to tip vortex formation, drag is decreased. In addition, the induced span-wise flow and up-wash from the propeller causes the span-wise lift distribution to remain more uniform at the wingtips, thus increasing the lift. Previous wind tunnel testing of this configuration has shown a significant increase in lift and decrease in drag, particularly in low-aspect-ratio configurations. In this paper the wind tunnel configuration is simulated by employing the tools of Computational Fluid Dynamics (CFD) in the ANSYS Fluent software. Several test cases are computed using 3D, transient, viscous, sliding mesh computational approach for the solution of Reynolds-Averaged Navier-Stokes (RANS) equations with SST k-ω turbulence model. CFD results match the wind tunnel data within approximately 1%, validating the CFD approach. For the wind-tunnel configuration, CFD results show that 18.1% increase in lift and 5.1% increase in net thrust is possible solely through the phenomenon of AWVC. This talk demonstrates that the CFD technology can be used for the analysis of more exotic UAV and aircraft configurations involving active wingtip vortex cancellation as well as distributed propulsion involving more propellers mounted on the wing.
Bio. Professor Ramesh K. Agarwal is the William Palm Professor of Engineering in the department of Mechanical Engineering and Materials Science at Washington University in St. Louis. From 1994 to 2001, he was the Sam Bloomfield Distinguished Professor and Executive Director of the National Institute for Aviation Research at Wichita State University in Kansas. From 1978 to 1994, he was the Program Director and McDonnell Douglas Fellow at McDonnell Douglas Research Laboratories in St. Louis. Dr. Agarwal received Ph.D in Aeronautical Sciences from Stanford University in 1975, M.S. in Aeronautical Engineering from the University of Minnesota in 1969 and B.S. in Mechanical Engineering from Indian Institute of Technology, Kharagpur, India in 1968. Over a period of forty five years, Professor Agarwal has worked in various areas of Computational Science and Engineering – Computational Fluid Dynamics, Computational Materials Science, Computational Acoustics and Electromagnetics, Control and Systems Theory, and Multidisciplinary Design and Optimization. He is the author and coauthor of over 600 journal and refereed conference publications. He has given many plenary, keynote and invited lectures at various national and international conferences worldwide in over fifty countries. Professor Agarwal continues to serve on many academic, government, and industrial advisory committees. Dr. Agarwal is a Fellow twenty two societies including the Institute of Electrical and Electronics Engineers (IEEE), American Association for Advancement of Science (AAAS), American Institute of Aeronautics and Astronautics (AIAA), American Physical Society (APS), American Society of Mechanical Engineers (ASME), Royal Aeronautical Society, Chinese Society of Aeronautics and Astronautics (CSAA), and American Society for Engineering Education (ASEE). He has received many prestigious honors and national/international awards from various professional societies and organizations for his research contributions including the AIAA Reeds Aeronautics Award, SAE Medal of Honor, ASME Honorary Membership and Honorary Fellowship from Royal Aeronautical Society.
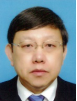
Keynote Speaker
Prof. Mingcong Deng
Tokyo University of Agriculture and Technology, Japan
Speech title: OPERATOR & LEARNING-BASED NONLINEAR CONTROL OF MICRO HAND AND ITS APPLICATION
Abstract: Soft actuators have been getting increased attention with developing of medical fields etc. A miniature pneumatic bending rubber actuator is one of the soft actuators. The actuator has the bellows shape and are made of silicone rubbers. Due to the bellows shape, the actuator can do two-way large bending by supplying positive or negative air-pressure. However, to control the actuator and make its model accurately are difficult because the actuator has nonlinearity. Moreover, the actuator should be controlled without sensor because its expected application are medical fields, especially, in operations. On the other hand, a control system based on operator theory can apply nonlinear systems with uncertainties. The relationship between operator theory and passivity or adaptive control which is an important idea in control engineering has discussed by some researchers. Meanwhile, support vector regression (SVR) has been utilized for classification and regression analysis, where the design parameters are selected by using particle swarm optimization (PSO). Therefore, operator-based control system is discussed. In order to realize sensorless control, PSO-SVR-based moving estimation with generalized Gaussian distribution (GGD) kernel is employed. That is, operator-based sensorless adaptive nonlinear control system considering passivity for the actuator and PSO-SVR-based moving estimation with GGD kernel are shown. Finally, some simulations and experimental results are introduced.
Bio. Prof. Mingcong Deng is a Professor of Tokyo University of Agriculture and Technology, Japan. He received his BS and MS in Automatic Control from Northeastern University, China, and PhD in Systems Science from Kumamoto University, Japan, in 1997. From 1997.04 to 2010.09, he was with Kumamoto University; University of Exeter, UK; NTT Communication Science Laboratories; Okayama University. Prof. Deng is a member of SICE, ISCIE, IEICE, JSME, IEEJ and the IEEE(SM). He specializes in three complementary areas: Operator based nonlinear fault detection and fault tolerant control system design; System design on thermoelectric conversion elements; Applications on smart material actuators. Prof. Deng has over 500 publications including 168 journal papers, 15 books (or chapters), in peer reviewed journals including IEEE Transactions, IEEE Press (for books) and other top tier outlets. He serves as a chief editor for International Journal of Advanced Mechatronic Systems, The Global Journal of Technology and Optimization, and associate editors of 6 international journals, including with IEEE journal. Prof. Deng is a co-chair of agricultural robotics and automation technical committee, IEEE Robotics and Automation Society; also a chair of the environmental sensing, networking, and decision making technical committee, IEEE SMC Society. He was the recipient of 2014 Meritorious Services Award of IEEE SMC Society.
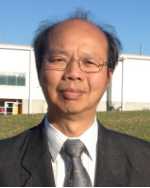
Keynote Speaker
Prof. John P. T. Mo
RMIT University, School of Aerospace, Mechanical and Manufacturing Engineering, Melbourne, Australia
Speech title: Manufacturing precision cutters from polycrystalline diamond, the hardest tool material
Abstract: In the last couple of decades, the concept of good product design has shifted from functionality to sustainability. With more customers demanding fuel efficiency, aircraft and automotive industries are using more composite fibre reinforced plastics (CFRP) materials in their products. However, CFRP materials are prone to delamination and local breakage if it is machined with cutter tools that are not sharp enough to cut with minimum forces. The unpredictable large variations in cutting forces damage the cutting edges easily if the tool material is not hard enough. Recently, polycrystalline diamond tools have been increasingly used in CFRP machining operations. However, polycrystalline diamond material is the hardest tool material and is extremely hard to grind to shape. In a complex product, thousands of accurate holes are required to be drilled. Similarly, complex profiles are shaped from the moulded CFRP components. Large number of ground and re-ground cutters are required to ensure these machining processes are completed with precision. Polycrystalline diamond tools have traditionally been ground by machinist who have developed great skills and dexterity in using their grinding machines. Armed with experience and an intuitive feel for the pressure needed to be exerted on the tool, they can take anywhere from four to five hours to grind one drill. While this exceptional skill is to be admired, such a time consuming and laborious process is clearly impractical to be duplicated for large scale production. Thus there is a need for a more efficient automated process. This paper reviews the development of a CNC grinding machine for polycrystalline diamond tools. Based on the principle of electric discharge erosion, several strategies for controlling the electric discharge process to produce high precision and reliable tools are discussed. Scientific findings and further research direction to advance the process are explained.
Bio. John Mo is Professor of Manufacturing Engineering in RMIT University, Australia since 2006. He was also Head of Manufacturing and Materials Engineering until 2014. Prior to this educational appointment, John was Project Manager in the Division of Manufacturing and Infrastructure Technology, CSIRO, Australia for 11 years. His team of professional research staff worked on numerous large scale international projects involving multi-disciplinary teams in the development of advanced manufacturing systems and the integration of global operations in aerospace, defence, national security and materials processing. John Mo received his first degree in Mechanical Engineering and Master in Industrial Engineering from the University of Hong Kong. He was awarded PhD from Loughborough University in 1989. Prior to migrating to Australia, John was Principal Lecturer in the City Polytechnic of Hong Kong. John has been an active member in professional engineering bodies including as Divisional Secretary of the Hong Kong Institution of Engineers, Chair of the Australian Chapter of the same institution, Mechanical Board Member of the Institution of Engineers Australia, and Committee Member of the Victoria Branch of the UK Institution of Mechanical Engineers. He was academic adviser to universities including Fiji National University.